Revolutionizing The Metalworking Industry 4.0: Embrace Innovation For Success Today!
The Revolutionary Metalworking Industry 4.0: Shaping the Future of Manufacturing
Welcome to the era of Metalworking Industry 4.0, where cutting-edge technology intertwines with traditional craftsmanship to revolutionize the world of manufacturing. This industrial revolution represents a significant leap forward in the metalworking industry, fostering advanced production processes, enhancing productivity, and promoting unprecedented levels of efficiency. As a passionate reviewer, I am thrilled to delve into the captivating world of Metalworking Industry 4.0 and share my unique insights and experiences.
What is Metalworking Industry 4.0?
Metalworking Industry 4.0 refers to the integration of digital technologies, automation, and data exchange in the manufacturing sphere. It encompasses a wide range of technologies such as artificial intelligence, robotics, Internet of Things (IoT), and cloud computing. This amalgamation of digital and physical systems allows for the creation of smart factories, where machines and humans work hand in hand to optimize production processes.
2 Picture Gallery: Revolutionizing The Metalworking Industry 4.0: Embrace Innovation For Success Today!
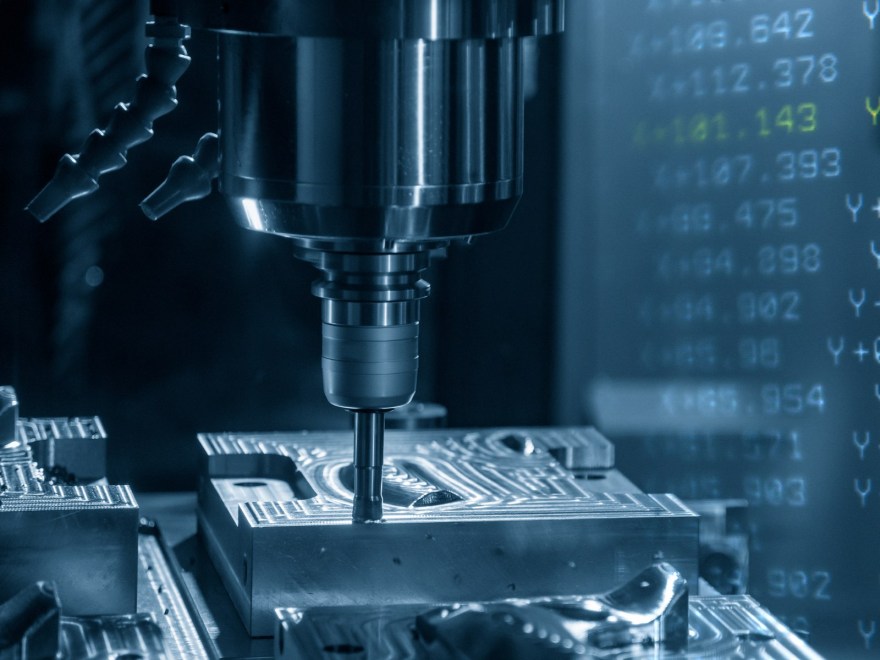
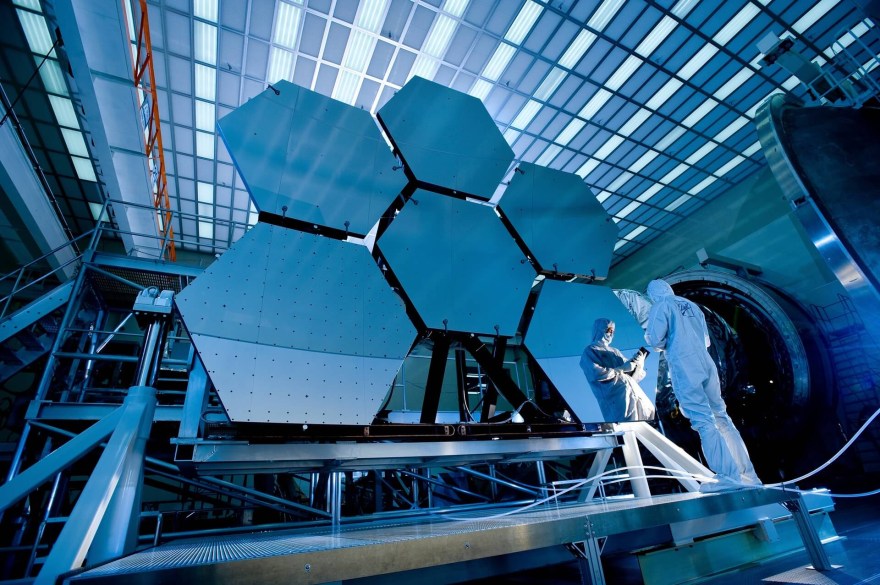
Who is Driving Metalworking Industry 4.0?
The driving force behind Metalworking Industry 4.0 is a collaboration between manufacturers, technology companies, and researchers. Visionary companies across the globe are investing in research and development to incorporate cutting-edge technologies into their operations. Additionally, renowned technology giants such as Siemens, General Electric, and IBM are spearheading the digital transformation in the manufacturing sector by providing innovative solutions and platforms.
When and Where Did Metalworking Industry 4.0 Emerge?
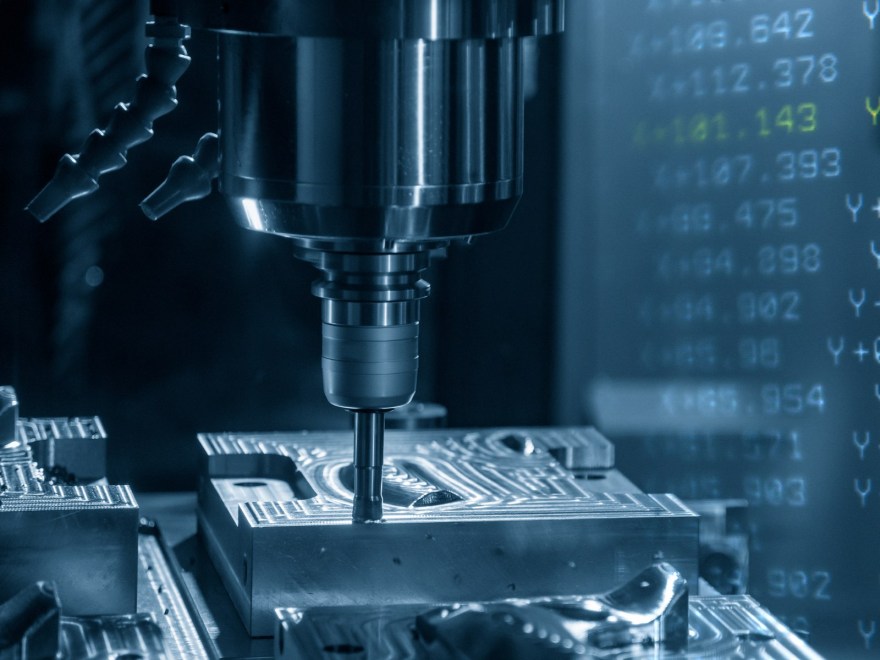
Image Source: evo-solutions.com
Metalworking Industry 4.0 emerged in the early 2010s as a result of advancements in connectivity, big data analytics, and machine learning. The concept originated in Germany and was officially introduced at the Hannover Messe trade fair in 2011. Since then, it has gained global recognition and has been adopted by manufacturers worldwide. Today, Metalworking Industry 4.0 is a key driver of innovation and competitiveness in the manufacturing sector.
Why is Metalworking Industry 4.0 Important?
Metalworking Industry 4.0 is of paramount importance as it holds the potential to revolutionize the manufacturing landscape. By leveraging digital technologies and automation, manufacturers can achieve unprecedented levels of efficiency, reduce costs, and enhance product quality. This transformation enables companies to remain competitive in an increasingly globalized and technologically driven market. Moreover, Metalworking Industry 4.0 fosters sustainable and environmentally friendly practices, minimizing waste and optimizing resource utilization.
How Does Metalworking Industry 4.0 Revolutionize Manufacturing Processes?
Metalworking Industry 4.0 revolutionizes manufacturing processes through the integration of smart sensors, data analytics, and machine learning algorithms. These technologies enable predictive maintenance, real-time monitoring, and intelligent automation. Machines equipped with sensors can collect vast amounts of data, which can be analyzed to identify patterns, detect anomalies, and optimize production parameters. This level of automation and intelligence enhances productivity, reduces downtime, and ensures consistent product quality.
Frequently Asked Questions about Metalworking Industry 4.0
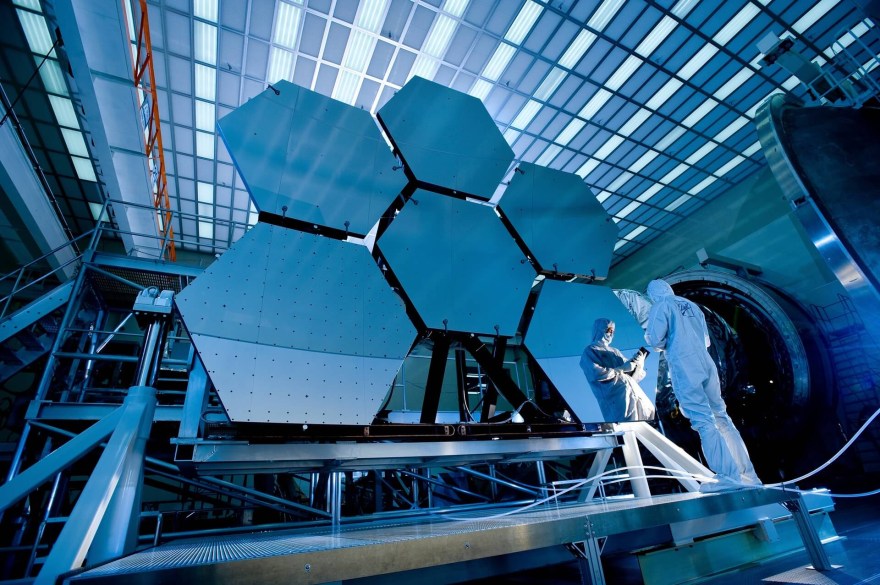
Image Source: apsolon.com
Q: What are the key technologies driving Metalworking Industry 4.0?
A: The key technologies driving Metalworking Industry 4.0 include artificial intelligence, robotics, Internet of Things (IoT), big data analytics, and cloud computing.
Q: How does Metalworking Industry 4.0 impact job prospects for workers?
A: While there are concerns about job displacement due to automation, Metalworking Industry 4.0 also creates new job opportunities in areas such as data analysis, system integration, and programming.
Q: What are the benefits of implementing Metalworking Industry 4.0?
A: Implementing Metalworking Industry 4.0 offers numerous benefits, including increased productivity, enhanced product quality, reduced costs, optimized resource utilization, and improved sustainability.
The Future of Metalworking Industry 4.0
The future of Metalworking Industry 4.0 is promising, with continuous advancements in technology and the adoption of innovative solutions. As manufacturers embrace digital transformation, they will unlock new possibilities for customization, mass customization, and agile production. The integration of virtual reality and augmented reality will further enhance training, design, and collaboration within the industry. The era of Metalworking Industry 4.0 is just the beginning of a remarkable journey that will shape the future of manufacturing.
Conclusion: A Paradigm Shift in Manufacturing
My journey into the world of Metalworking Industry 4.0 has been nothing short of awe-inspiring. The convergence of cutting-edge technology and traditional craftsmanship has paved the way for a new era in manufacturing. Metalworking Industry 4.0 offers unparalleled opportunities for manufacturers to streamline their operations, improve efficiency, and create innovative products. As a reviewer, I wholeheartedly recommend embracing this industrial revolution and exploring the endless possibilities it brings. Welcome to the future of manufacturing!
This post topic: Metalworking